Ovviamente si stà parlando di "autocostruzione reale", non di acquistare questo e quello e poi metterli insieme, a quel punto conviene acquistarli già fatti.
Uno dei problemi da affrontare è quello del contenitore. Serve un contenitore di una certa forma e dimensione, che tutti più o meno abbiamo visto in rete su foto e listini, resistente all'acido solforico diluito, robusto quanto basta a contenere diversi chili di piombo (che pesa un accidente....). Fatto con materiale facilmente reperibile, a basso costo e facilmente lavorabile. Un po' come "pescare la Luna nel pozzo".....

Tra le materie plastiche adatte a resistere all'acido solforico diluito risulta esserci anche il PVC. Mettendo a posto del materiale d'avanzo ai tanti lavori fatti a casa in passato mi sono capitati tra le mani dei pezzi di tubo in PVC per scarichi, quel tubo di plastica gialla rigido e pesante che si usa in edilizia per le condotte di scarico dei bagni. E' malleabile al calore...... E da quì l'idea!
Avevo soltanto tubi del diametro di 100mm (ma si trovano anche di più grandi) e sono partito da uno spezzone di questo per fare un prototipo.
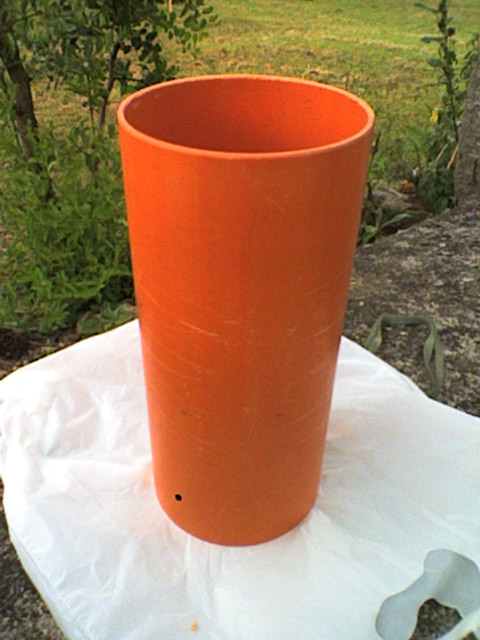
Purtroppo è rotondo..... Non adatto a poterci infilare dentro piastre piane, per cui bisognava "squadrarlo".
Per fare questo necessita di una forma su cui infilarlo dopo scaldato. Ho realizzato una forma in legno a sezione rettangolare con un pezzo di legno da costruzione tagliato e piallato, di perimetro uguale allo sviluppo della circonferenza interna del tubo. Nel caso specifico 95mm, che per pigreca sono circa 300mm. La forma ha naturalmente gli angoli leggermente smussati, per cui da 2 prove fatte risulta che il parallelepipedo deve avere (ma sono misure arbitrarie fatte per prova....) i lati di 100x55mm.
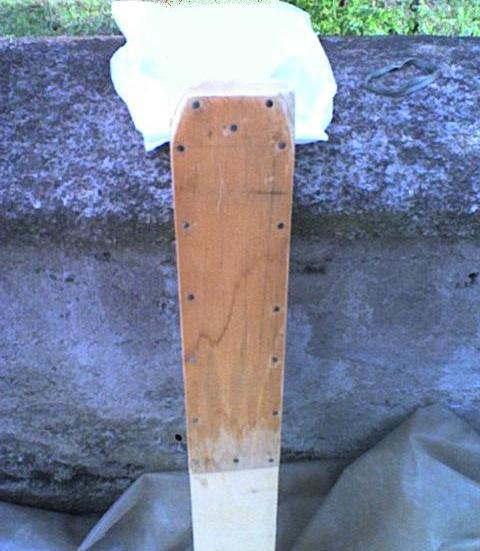
Lo spezzone di tubo va riscaldato. Io ho usato il forno di una vecchia cucina a gas in disuso, ma nessuno vieta di usare sistemi diversi. Ho infilato il pezzo di tubo su una stecca di legno di lunghezza adeguata a poter essere sorretta dalle guide interne del forno. Se avesse toccato intorno avrebbe rischiato di bruciarsi.
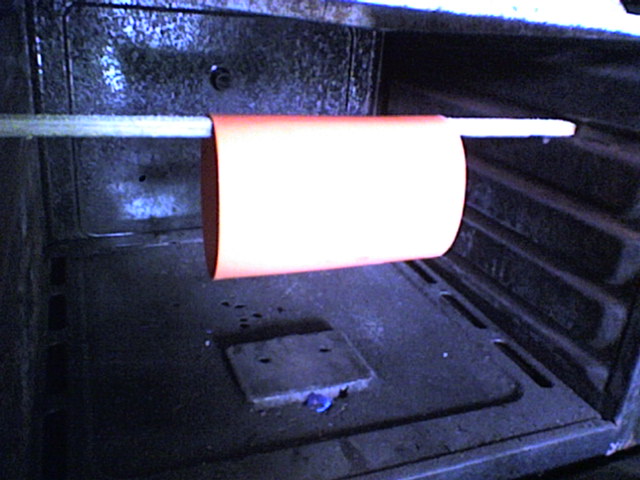
Quando il vecchio termometro incorporato nello sportello del forno è arrivato intorno ai 150°C (come si vede nella foto sotto) il tubo si è completamente ammorbidito. Probabilmente quel termometro non funziona più bene, per cui la temperatura è puramente indicativa.
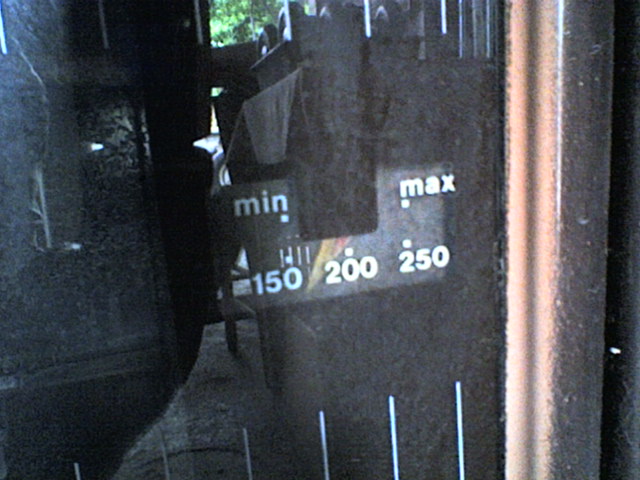
Girato un paio di volte intorno al legnetto per uniformare la temperatura, l'ho poi infilato velocemente sulla forma, stringendolo contro il legno. Naturalmente si lavora coi guanti, altrimenti ci si spellano le dita.

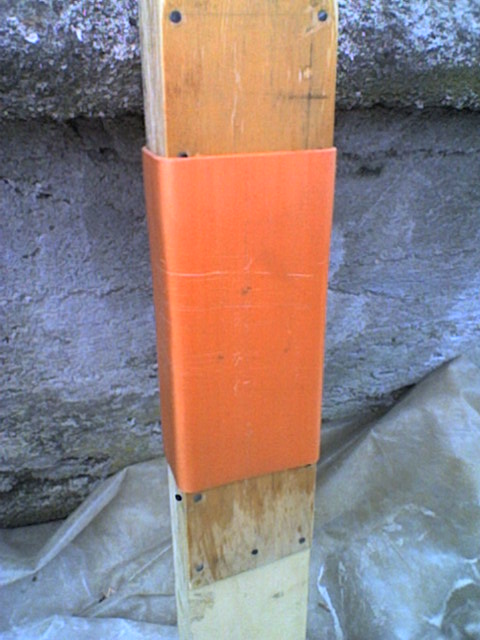
Ho ripetuto due tentativi, realizzando due parallelepipedi, uno un po' più lungo dell'altro.

Quello più lungo, il secondo, è uscito meglio, e ho deciso di usarlo per la prova. Così ad occhio aveva anche delle misure migliori e più "somiglianti" alle proporzioni degli elementi nelle foto.
A quel punto mi servivano dei ritagli di lastra di PVC con cui fare i fondi e le altre parti, per cui preso un altro spezzone di tubo l'ho segato da una parte col seghetto per ferro nel senso della lunghezza, poi messo sulla solita stecchetta nel forno l'ho fatto rammollire ben bene e pressato tra due lastre di vetro spianate, con dei pesi sopra.

Credo si veda dalle foto che questo spezzone di tubo era.....Usato.
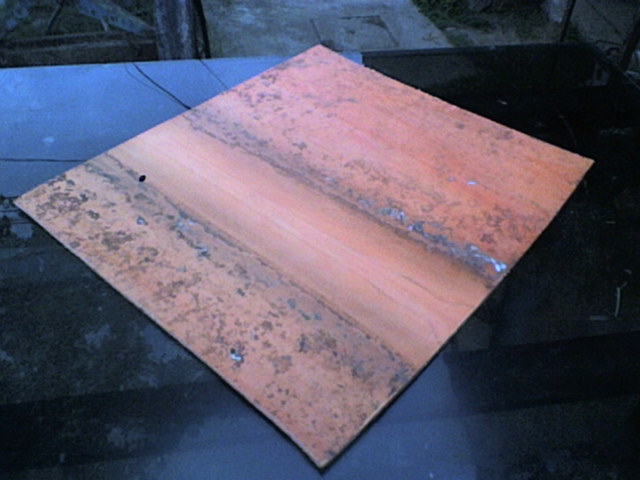
Però questi tubi in PVC sono praticamente inattaccabili da qualsiasi composto organico, anche dopo molto tempo, per cui passata un po' di cartavetrata e di lana d'acciaio la lastra è tornata pulita.

Con squadra, lima, seghetto, truschino (oppure penna, o matita) e forbici da lattoniere si traccia e si taglia la lastra, si rifinisce sui bordi o si mussa dove serve.
Ho cominciato incollando all'interno, dalla parte che poi sarebbe diventata il fondo, i rialzi di sostegno delle piastre, realizzati con rettangolini alti 3cm.

La colla usata è il solito Tangit, credo usato un po' dovunque, ma nulla vieta di usare prodotti di uguale efficacia. In genere asciuga subito, ma usata in spessori forti come in questo caso necessita di un po' di tempo per indurire completamente, non meno di 24 ore, per sicurezza. Comunque lì per lì risulta abbastanza "veloce" da non intralciare il montaggio dei pezzi.
Incollati i tre sostegni per le piastre di piombo, ho applicato il "fondo" del contenitore, incollandolo sia sui bordi esterni che sotto i sostegni, poi ho ripassato un bel cordone spesso di collante tutt'intorno al perimetro del fondo in modo da irrobustire il tutto e renderlo perfettamente stagno.

Di piastrine come quella usata per il fondo ne ho fatte tre. Una delle altre è stata forata al centro per un eventuale tappo, e usata come coperchio, la terza è stata ritagliata al centro per essere usata come bordo di rinforzo superiore, ma immagino che la foto sia meglio di qualsiasi spiegazione.

Si vedono i sostegni sul fondo, e il coperchio col buco, messo in piedi per sorreggere la scatola per fare la foto. Intorno al foro ho incollato tre rondelle dello stesso PVC, le une sulle altre, per formare una specie di "collo" in cui infilare un tappo di sfiato recuperato da una delle tante batterie demolite per prendere il piombo. Un paio di tappi differenti sono lì vicino.
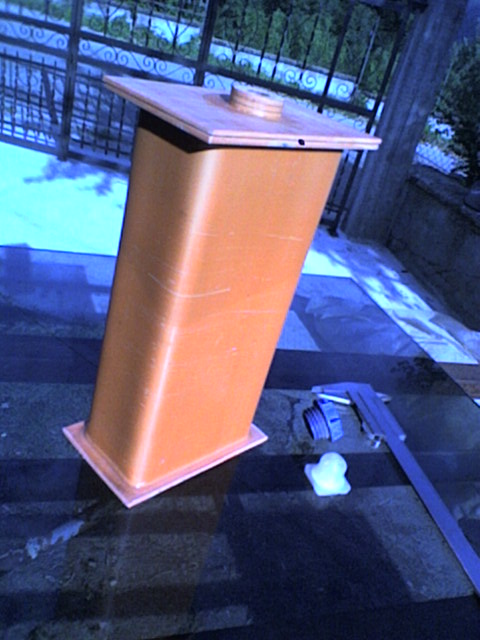
Nella foto sopra si vede il contenitore finito (o quasi.....). Manca solo di allarghare il foro per il tappo e una mano di vernice alla nitro per cambiare il colore.

Ci vorrebbe una guarnizione sotto il coperchio, di qualche tipo di gomma morbida che non viene attaccata dall'acido, o magari del silicone.
Visto che si trattava di una realizzazione di prova, alla fine ho deciso di non aggiungere niente.
Mi sono limitato ad allargare il foro del coperchio, per poterci mettere un tappo con sfiato di recupero, e passare una mano di vernice grigia, residuo in una bomboletta che usavo per i ritocchi alla buon'anima del defunto A112 di famiglia.

La "buccia d'arancia" è compresa nel prezzo, e le scolature di vernice sono omaggio della ditta. Verniciare a spruzzo è una delle tante cose che non sono capace di fare..... (un'altra è fare soldi

Volendo irrobustire il fondo del contenitore non dovrebbe essere difficile. Si può realizzarlo con lastra piegata e incollata anche sui lati, o aggiungendo rinforzi in diversi altri modi.
In un futuro prossimo voglio riprovare con tubo più grande, da 25cm di diametro, che si tradude in 78cm di circonferenza, squadrati nel modo usato sopra potrebbero venire dei contenitori molto simili a quelli commerciali da 400Ah.
Ovviamente trattandosi di Planté autocostruite mi accontenterei anche solo della metà della capacità, alla fine........
